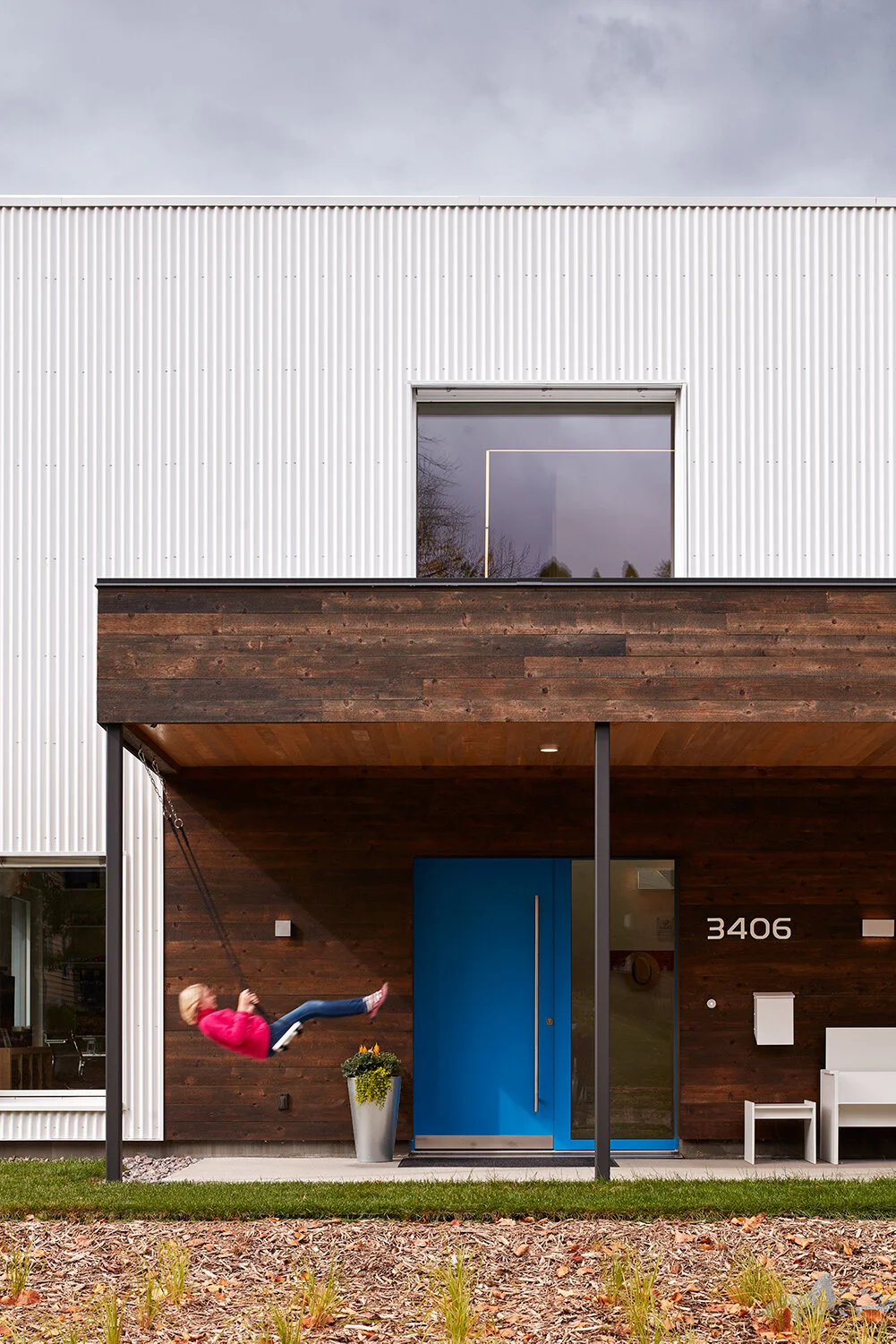
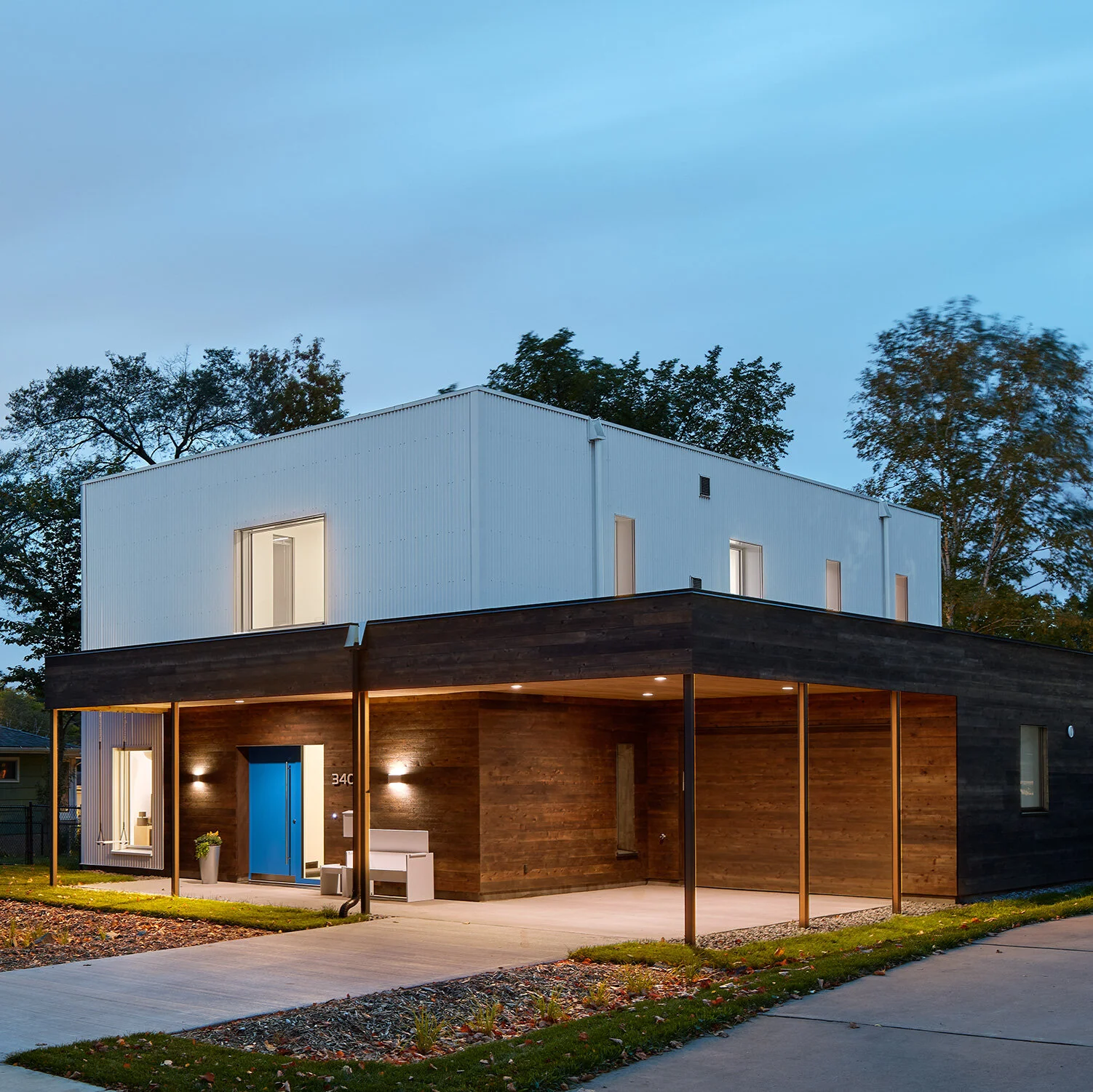

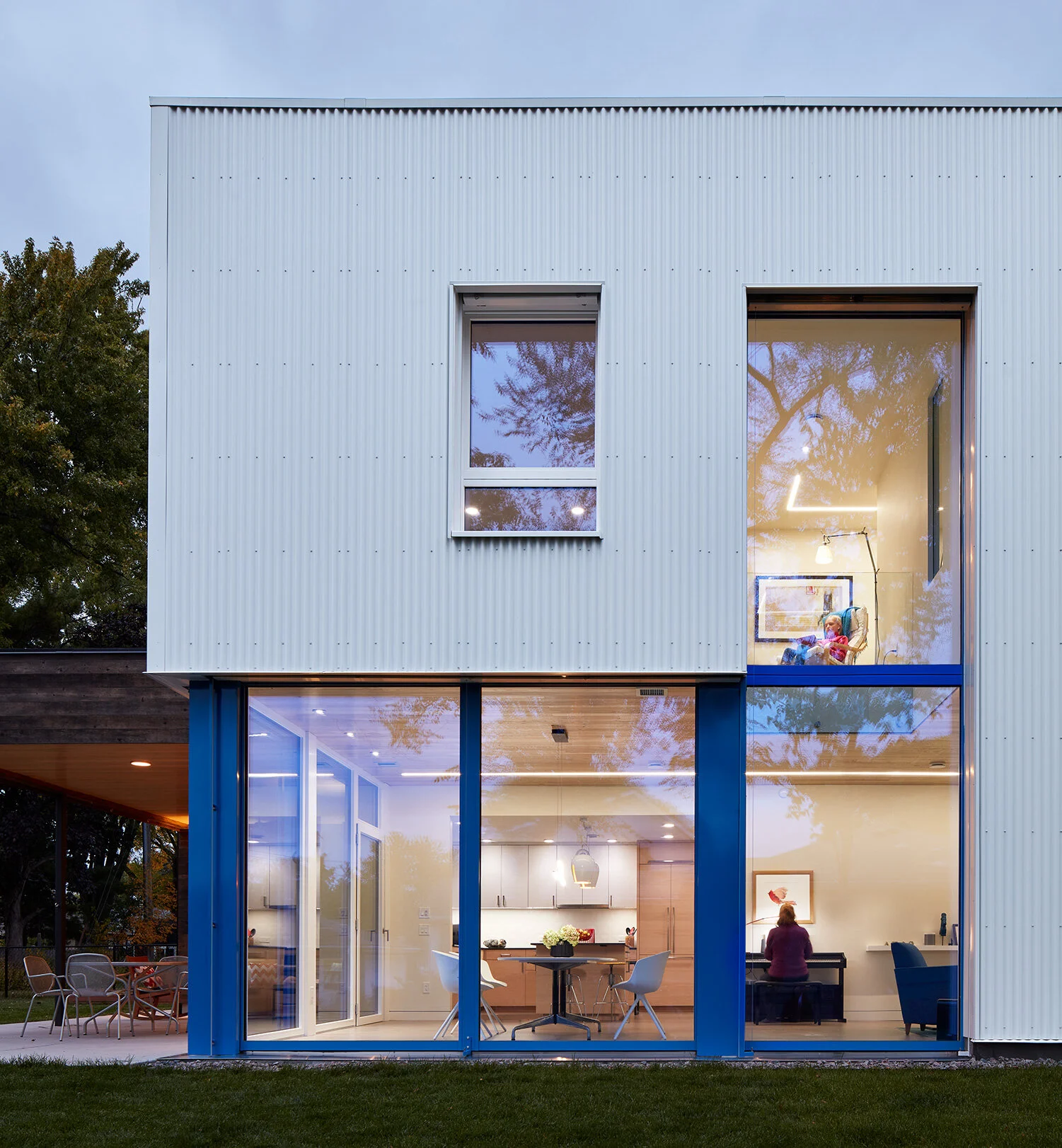
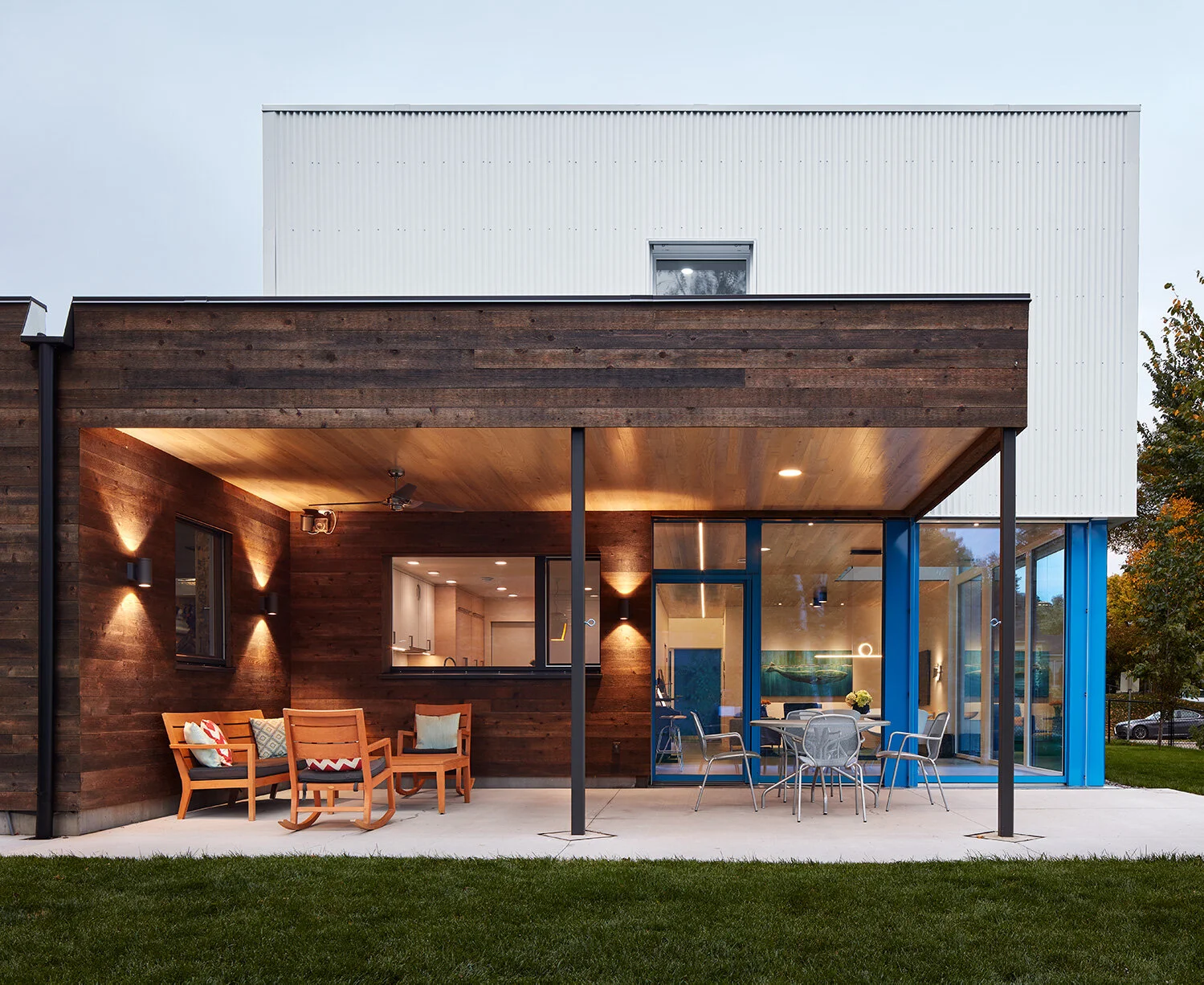
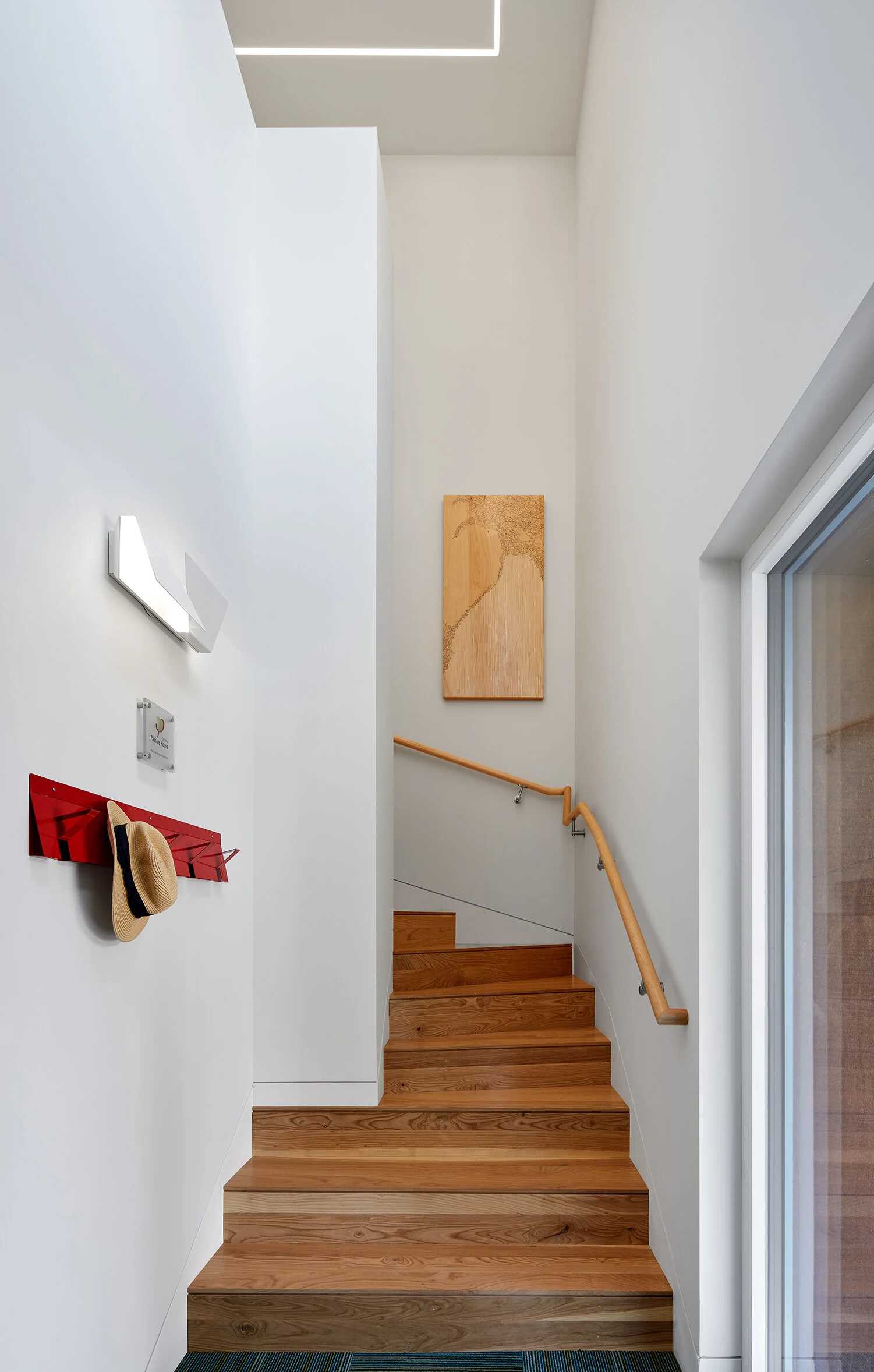





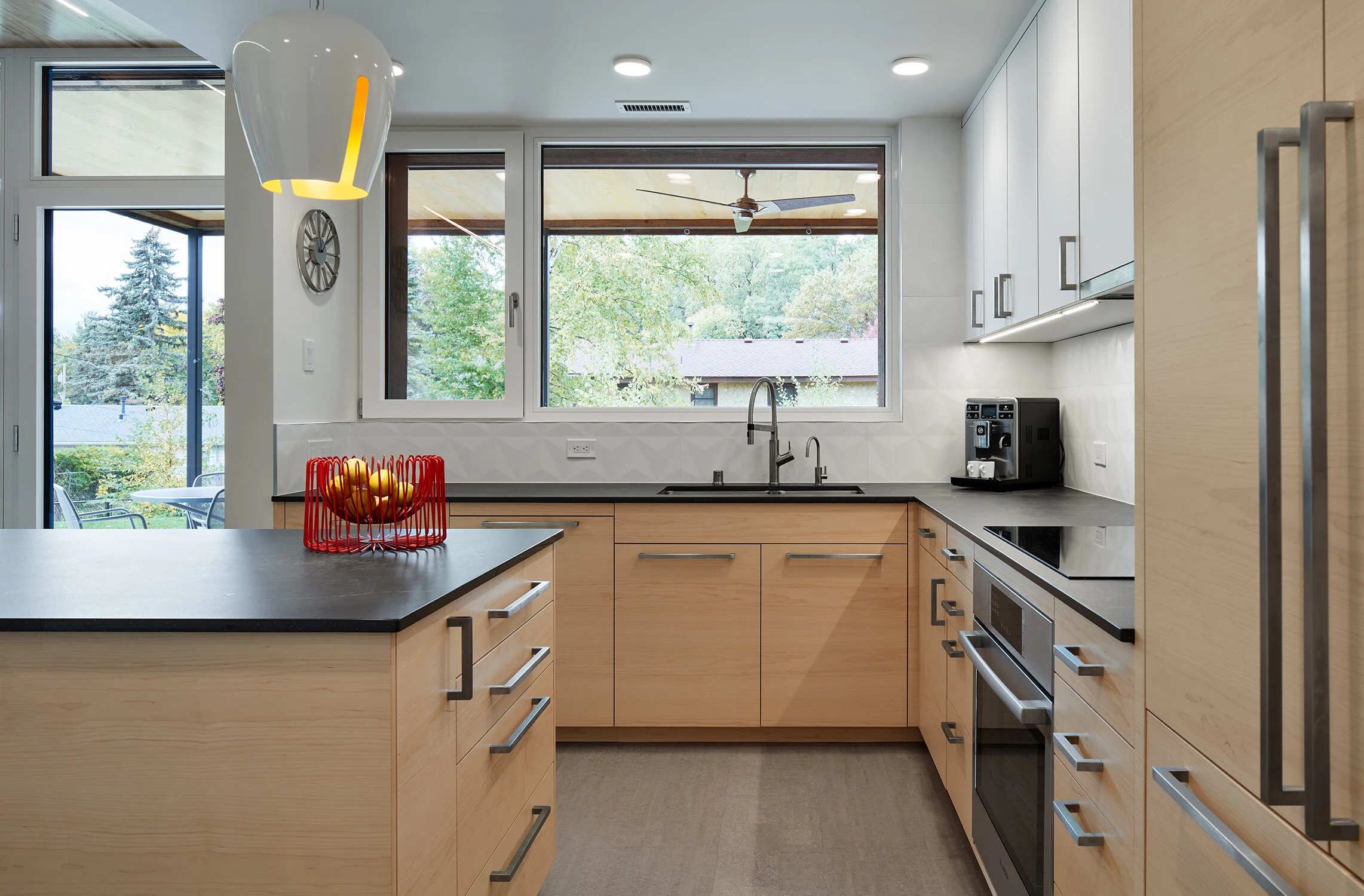

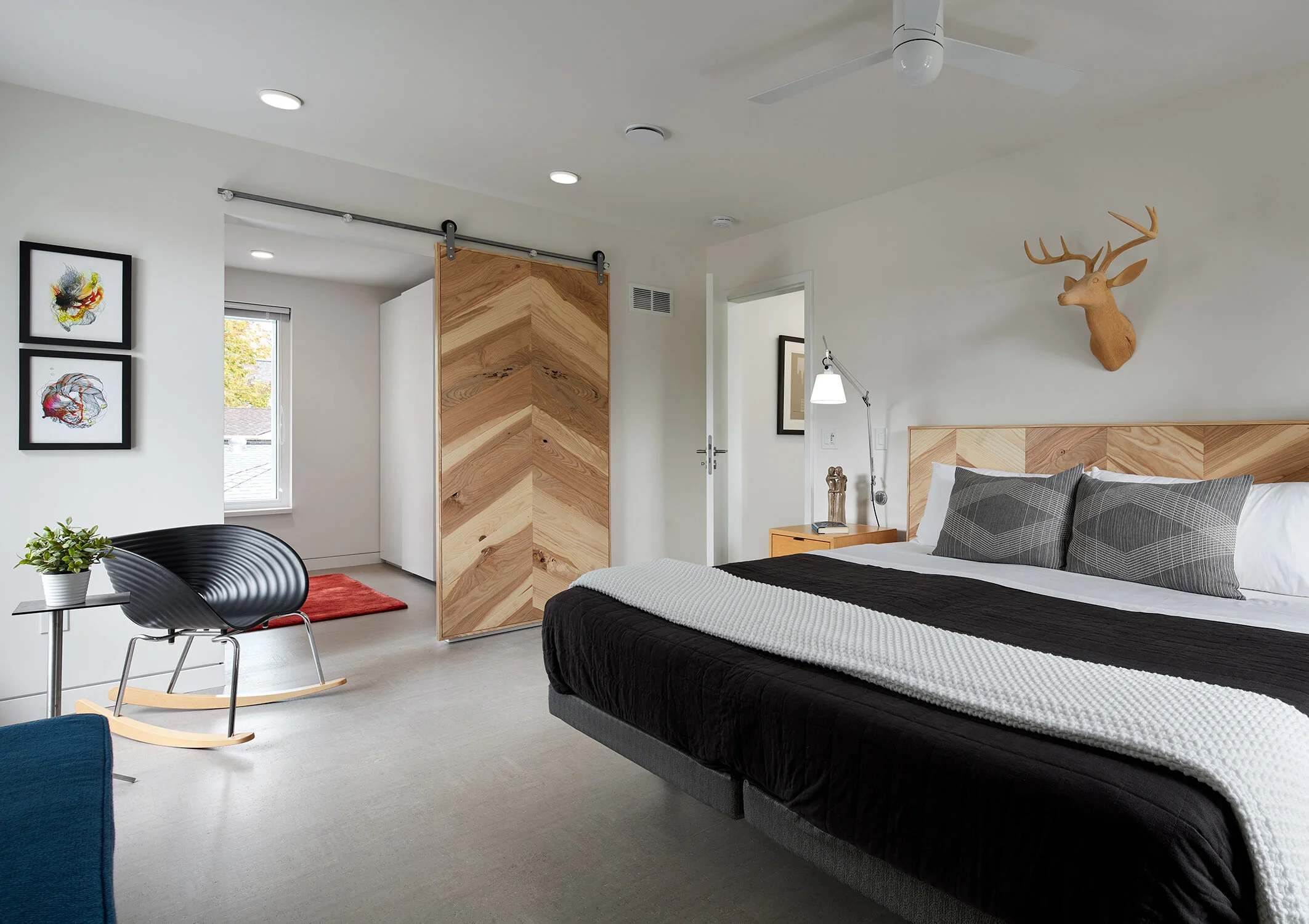

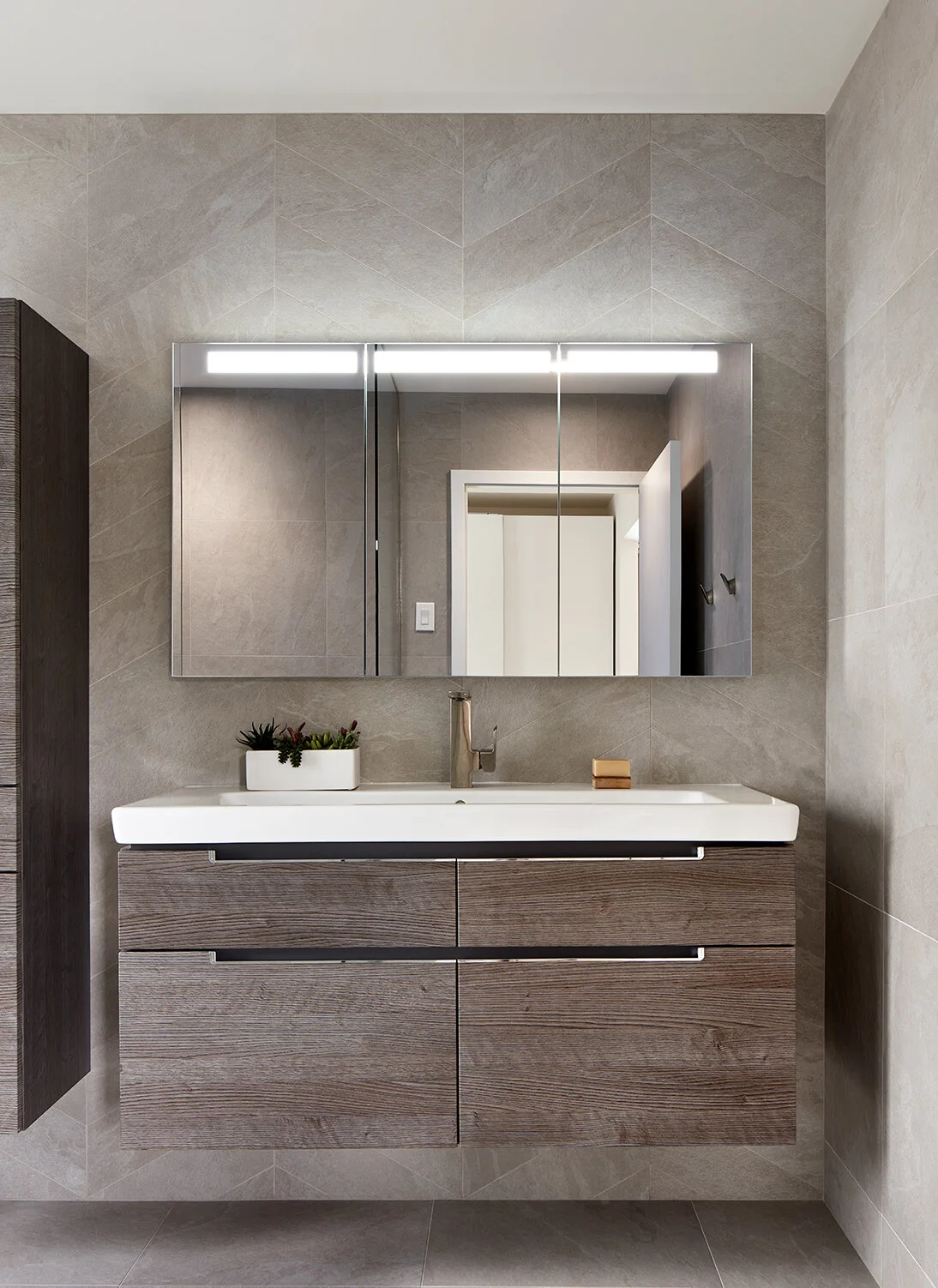
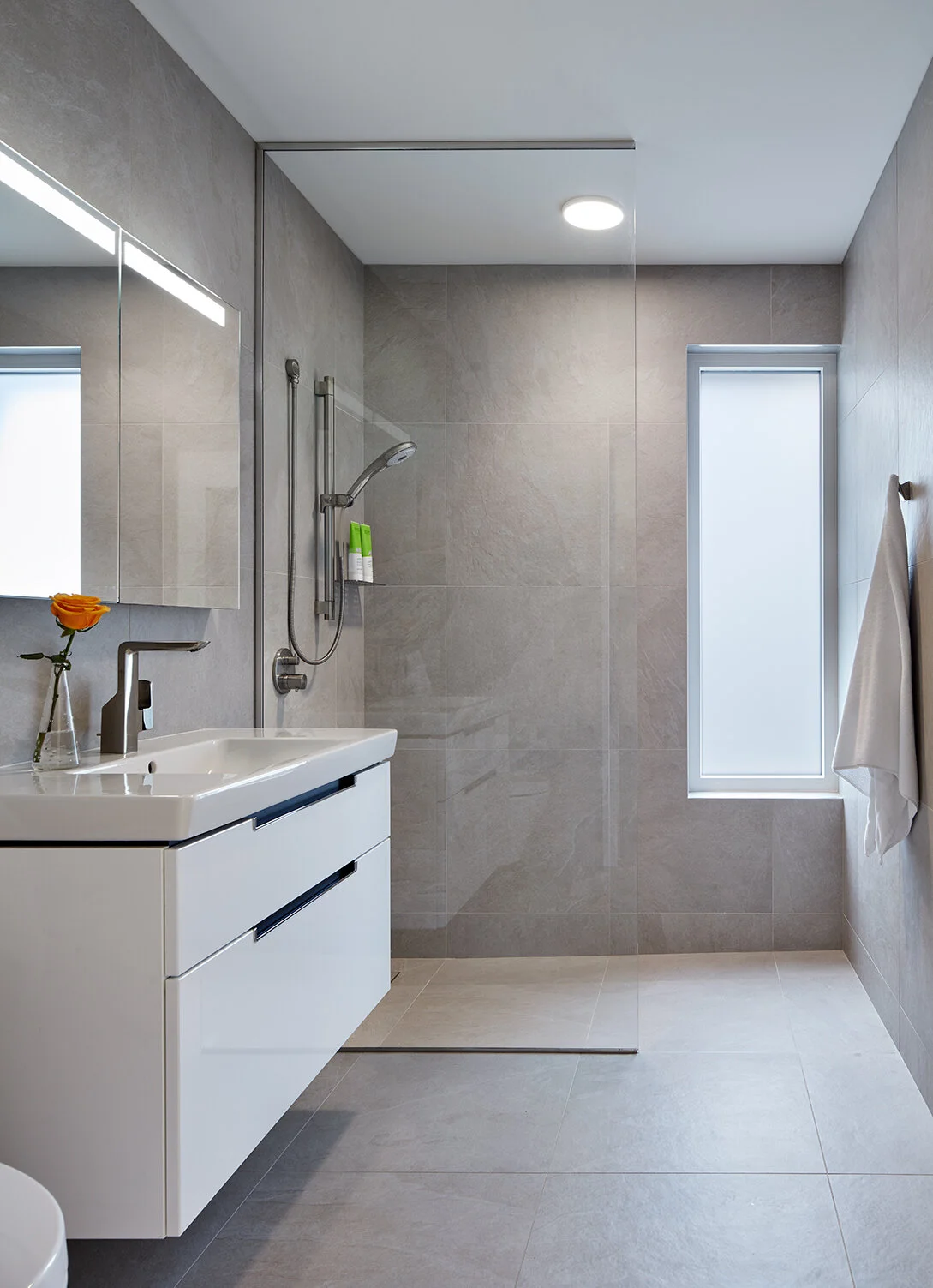
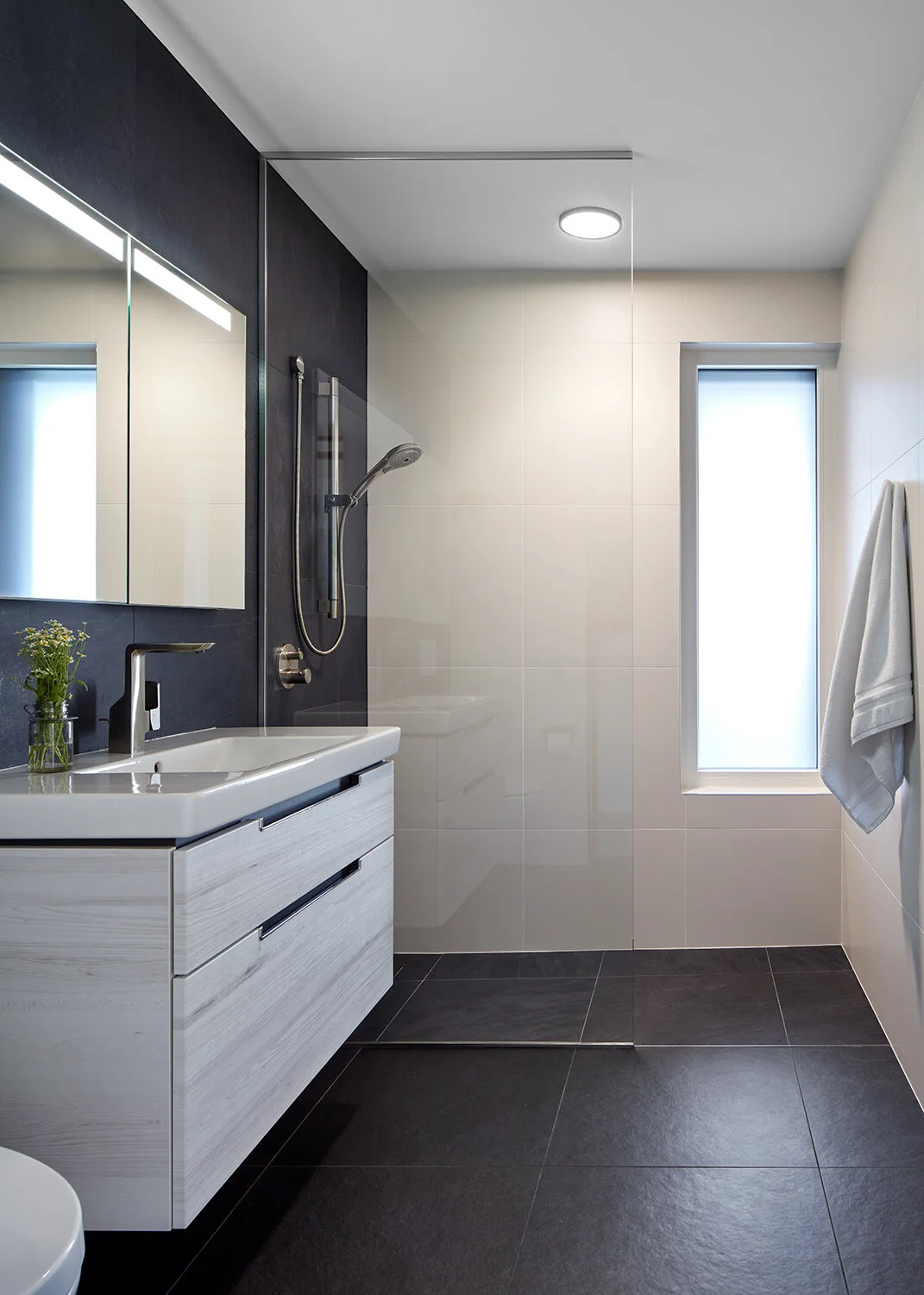
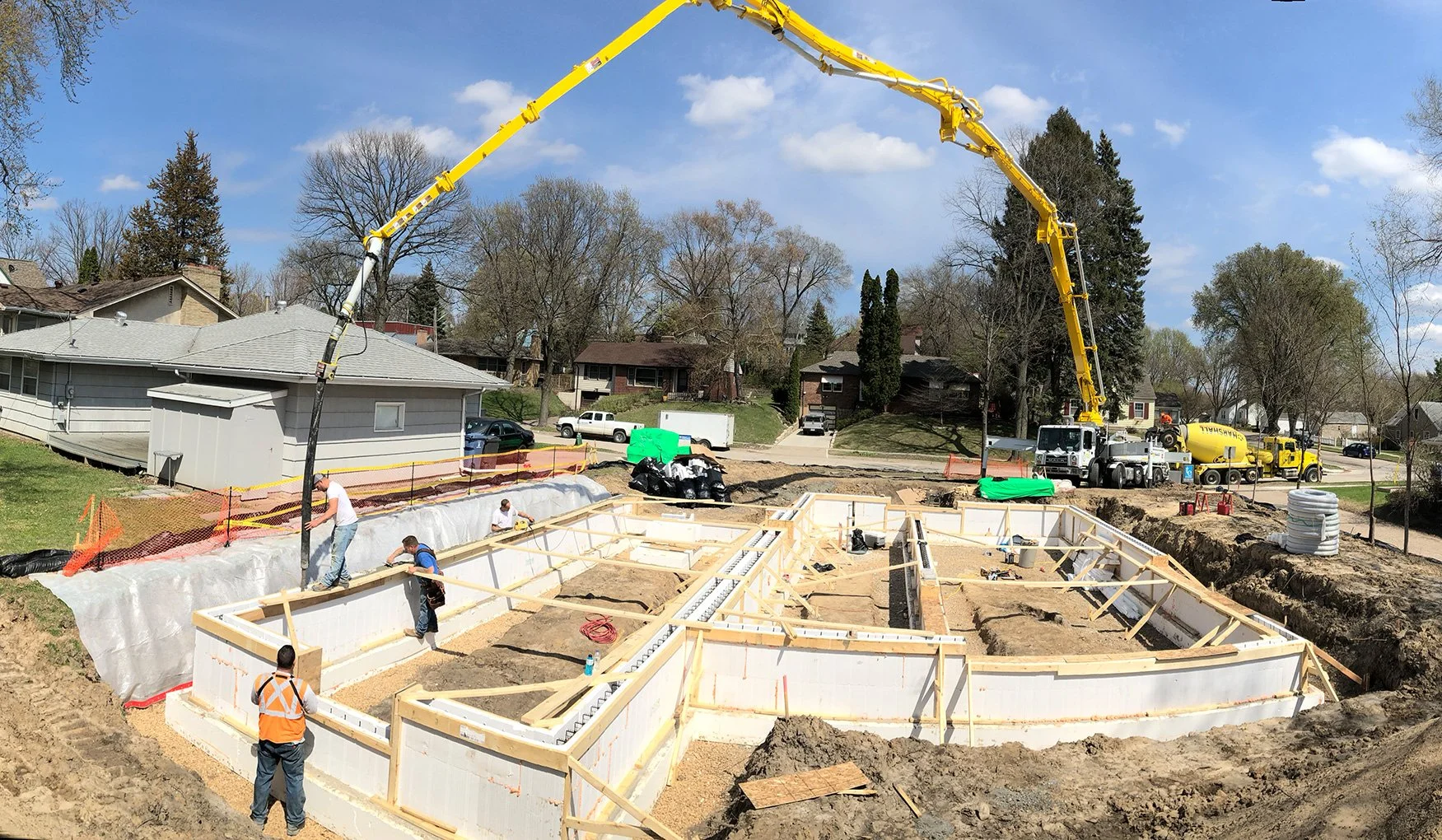
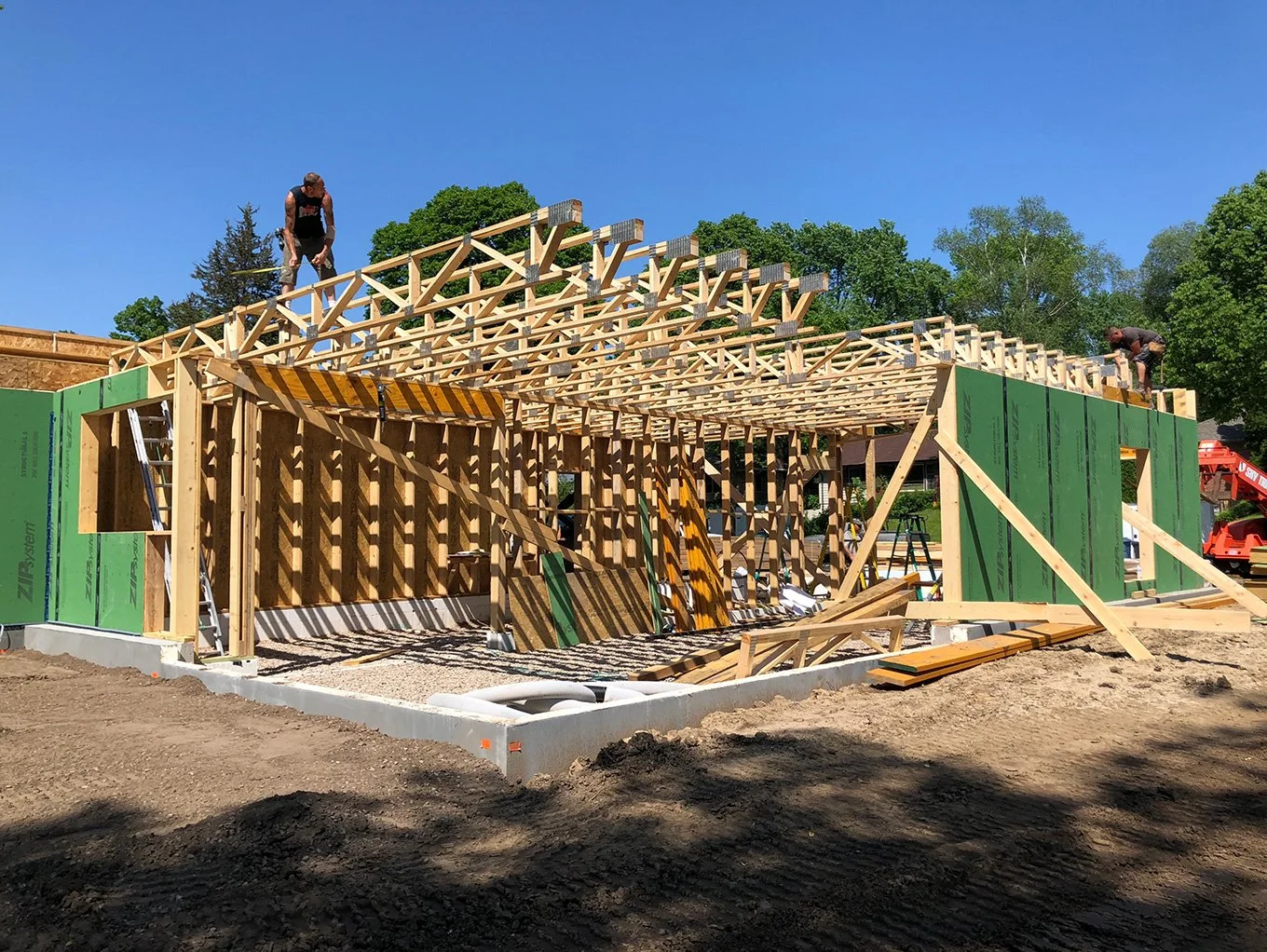
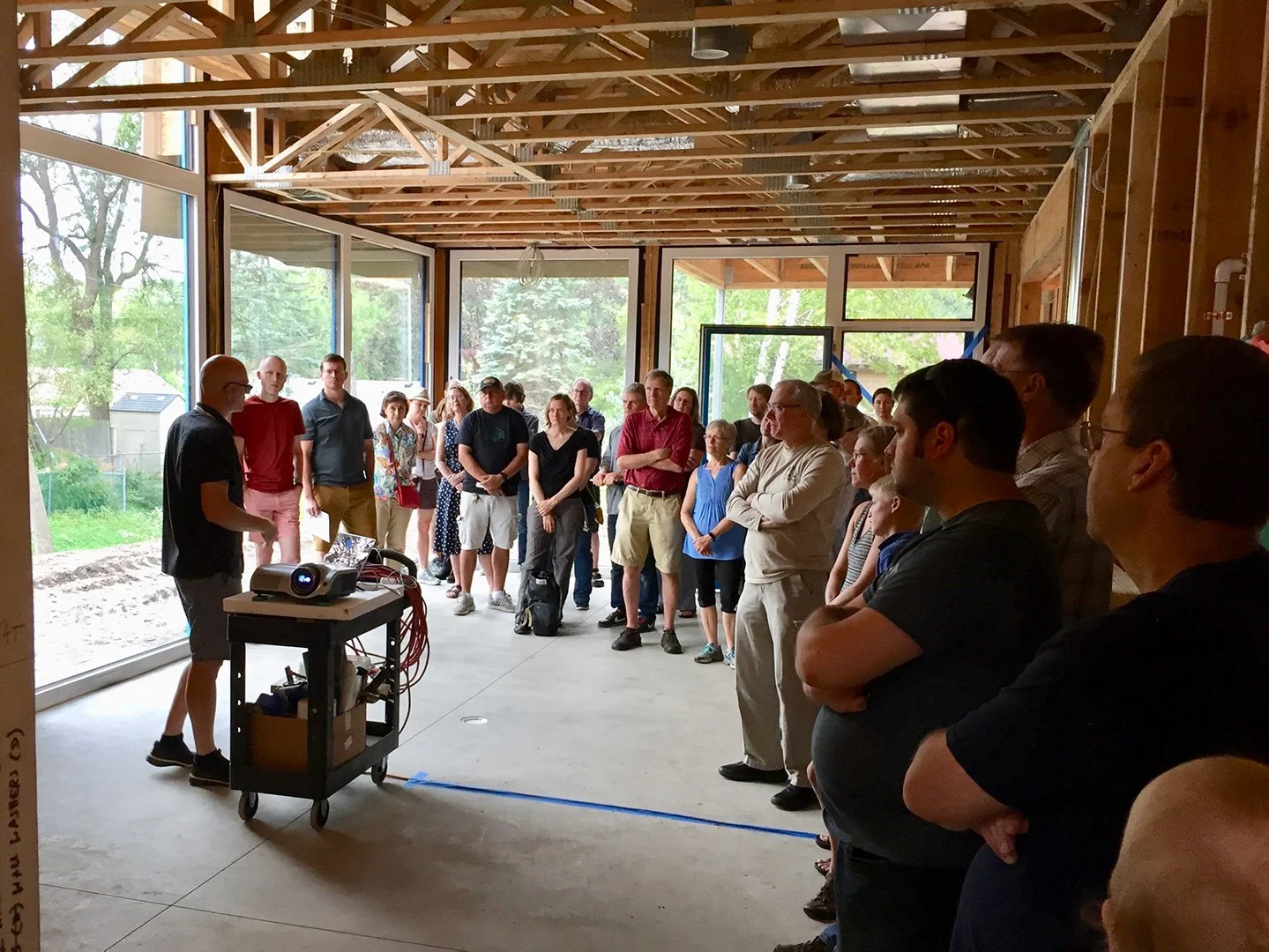
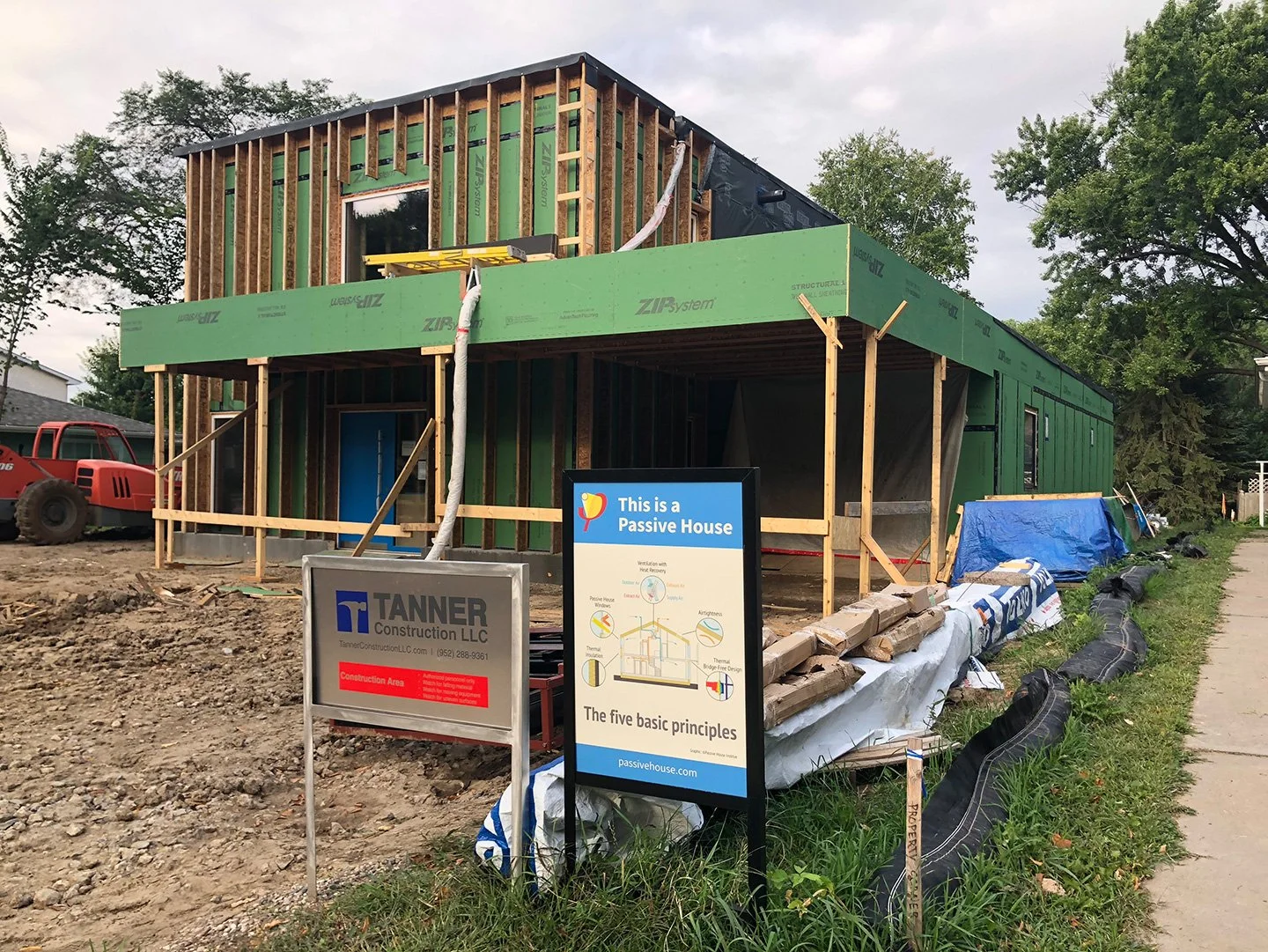
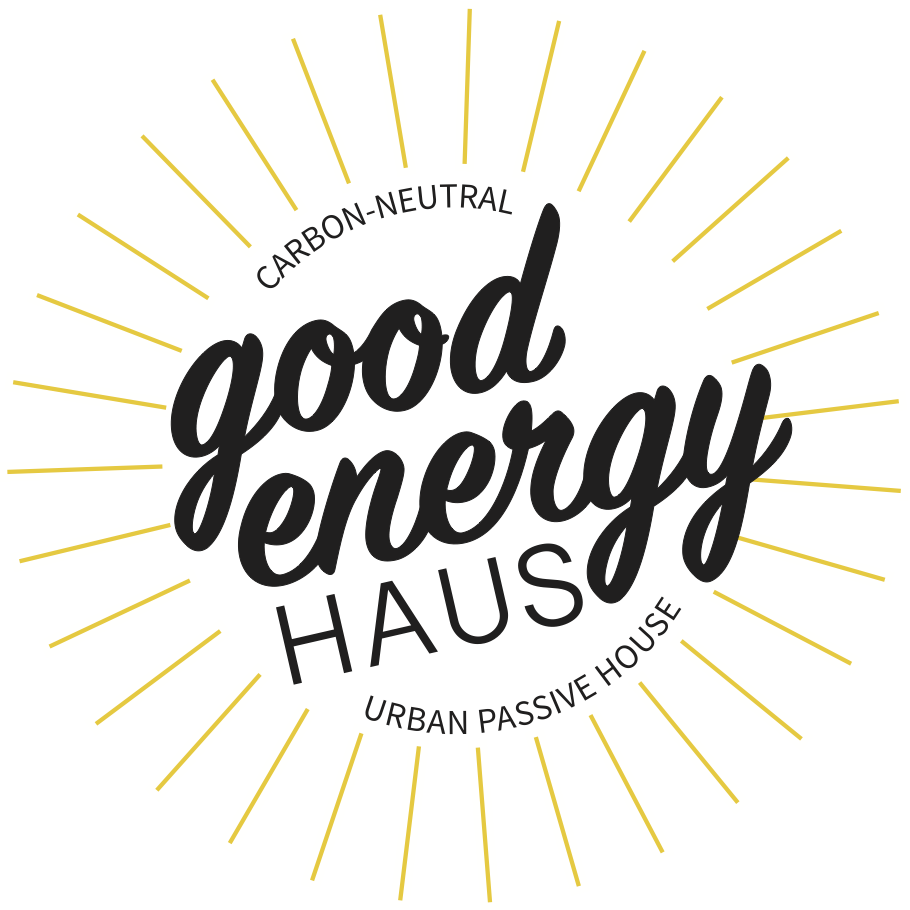
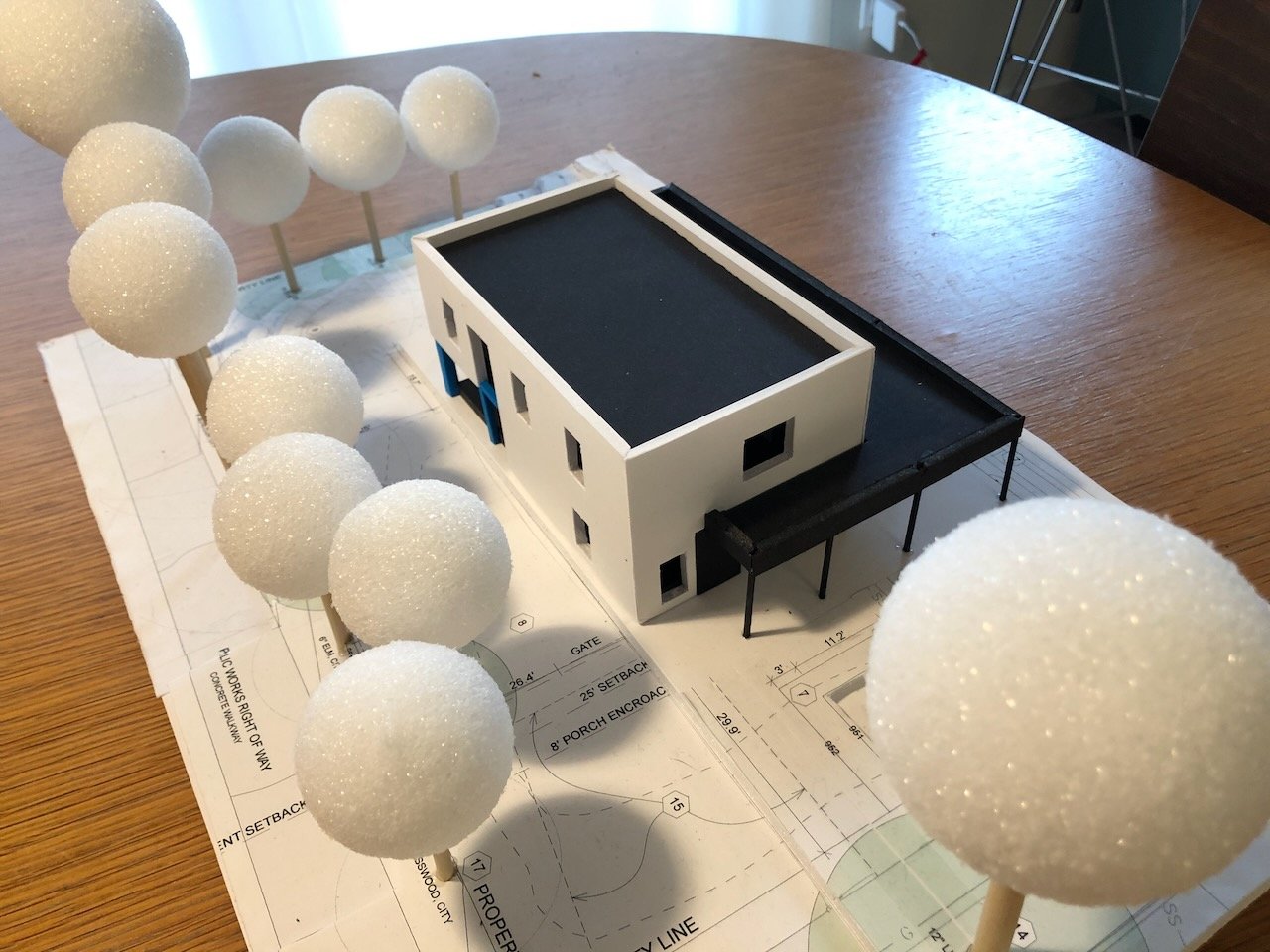
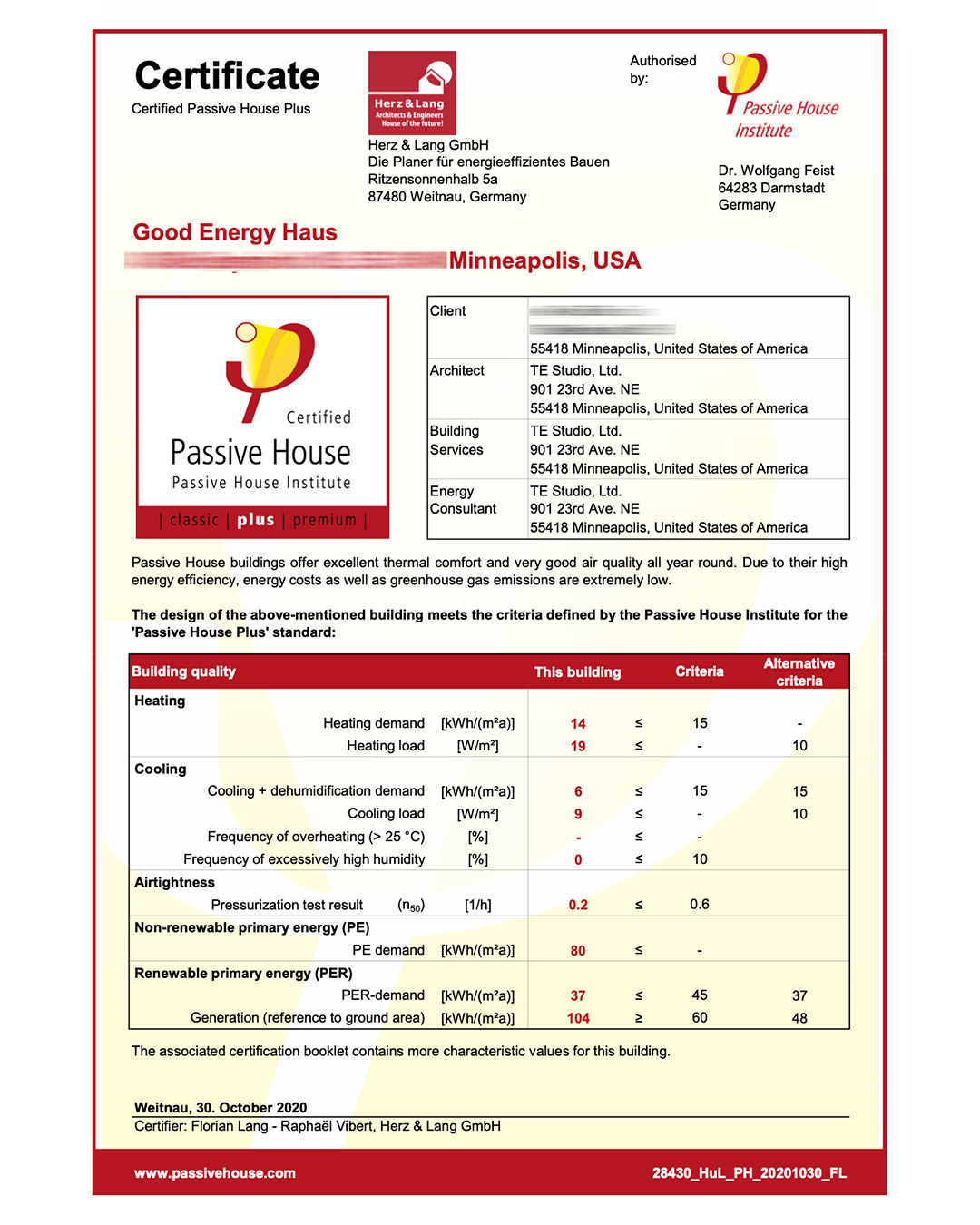
Good Energy Haus
The first urban infill, climate-neutral, certified Passive House Plus in Minneapolis.
Designed by TE Studio principal Tim Delhey Eian as his family home, Good Energy Haus was built in 2019/20 and serves as a beacon for sustainability, as well as a demonstration showcase for the design firm and its partners. This 2,150 square foot urban infill home is a case study for modern, sustainable, and climate-neutral living in Minneapolis, Minnesota. Tim has a long history with Passive House in North America. Successfully completing the first North American Passive House training in 2008, and designing the third certified Passive House project on the continent, his TE Studio has entirely focused on Passive House designs ever since. Tim is the founder of Passive House Minnesota, a chapter of the Passive House Network and the international Passive House Association. The story and path of the Good Energy Haus was shared extensively with the community by Tim Eian and TE Studio throughout the design and build processes.
Story
The Good Energy Haus replaces a home that was severely neglected; eventually boarded and condemned. The only path forward for the property was a teardown in late 2018 at the order of the City. Having lived on the same block for many years, Tim could easily envision a Passive House design for this double city lot. Design for a modern, resilient, 2-story, 4-bedroom, 3-bath Passive House Plus began almost immediately after taking possession in late 2018. Then however, things slowed down due to the harsh Minnesota winter. While designed in a record time, Tim and his family had to patiently await the spring of 2019 to begin construction.
Permitting also became a challenge as archaic and backward-facing ordinances in Minneapolis challenged the modern Passive House design, and the lack of a back alley required variances from City rules to approach the site from the front by car. Working with the staff and elected officials through these challenges, Tim and his wife prevailed and construction officially started on April 14, 2019.
The rest, as they say, is history, and while the story of move-in during the first Covid lockdown in March 2020 rivaled the effort of an iron-man competition for the family, the home was eventually “mostly” finished during the turmoil of the beginning of the pandemic, and followed up by “shelter-in-place” with parents and kids being confined to the building for much of the first year of occupancy with both work and schooling happening remotely from home. Construction efforts eventually concluded in May 2020—basically a year after they started. Landscaping began thereafter, as did the installation of the solar photovoltaic system on the roof, which was completed in December 2020.
First Floor Plan
Design
Good Energy Haus’ zero-step (accessible) first floor features an open living area, kitchen, mudroom (with access to the attached 2.5-car garage), guest bedroom/ home office and ¾ bath. The second floor holds two smaller bedrooms with a shared bath on the east side. A generous hallway connects a vertical space at the stair with an interior balcony overlooking the great room. A centrally located laundry room doubles as storage on this floor in the center north. The master suite completes the layout on the west side with a generous bedroom area, a walk-through closet and master bath. In total, the home offers about 2,150 finished square feet on two floors, and 670 square feet of attached, conditioned garage space. Both front and backyard feature generous covered outdoor areas for enjoyment, entertainment, projects, and to keep snow and debris from the accessible, zero-step entries. The main floor is designed for aging-in-place.
The design is simple and well-proportioned with a focus on function and flow, as well as space where it counts most, while not being large. From cork floors to reclaimed Ash-wood ceilings and stairs, materials and finishes were selected with regards to environmental and human impact. The exterior is resilient with metal panel siding where the home is hard to reach for maintenance, and locally sourced rough-sawn Cedar wood siding where it is within reach. Windows were sourced from Germany, which is typical for cold-climate Passive House projects in the US due to the quality and performance on offer in central Europe that is not being achieved by locally manufactured products at the time of writing. East, west and south-facing windows feature exterior motorized shades for sun-control.
The home is wood-frame construction with studs spaced 24 inches on center to reduce the structural wood content and maximize insulation levels. The double-wall is about 20 inches thick from inside to outside—filled with dense-packed Cellulose insulation. All siding is back ventilated. The stem walls are insulated concrete forms with an exterior insulation finish system and footed at frost levels of roughly 3-½ feet below grade on top of fully insulated perimeter footings. The roof is low-sloped and covered in an EPDM membrane. Downspouts are routed to raingardens on site for nearly 100% infiltration of stormwater on site.
The building envelope does most of the heavy lifting to keep the interior at room temperature. The “backup” mechanical system is made up of a cold climate air source heat pump for home and garage, with a dehumidifier for the home. The house is ventilated by a balanced, whole-house enthalpy recovery ventilation system. Hot water is being generated by a tanked indoor air-to-water heat pump, and augmented by a waste-water heat-recovery pipe, which captures the second floor drains. The exterior shades are controlled by a home automation system, which also provides thermostat and humidity controls, as well as some other amenities.
Second Floor Plan
Take a quick tour.
In June 2020, Tim Eian created a brief video tour for the Passive House conference.
In July of 2022, Smart Home Tours featured the house on its Youtube channel.
Enjoy!
Good Energy Haus - Tour June 2020
Partnerships
The Good Energy Haus is made possible by contributions from our awesome project partners. Please learn more about them by visiting their websites.
Construction
Passive House construction: Tanner Construction
Custom cabinetry: Nest Woodworking
Electrical: Koppi Electric
Building performance testing: DPIS
Passive House certification: Herz & Lang
Fixtures and Finishes
Villeroy and Boch, Toto, Blanco and Mountain Plumbing fixtures via North Central Sales
Wood From The Hood reclaimed wood
Dekton countertops via Consentino with installation by Stone Systems
Lea Ceramiche tile by Tile x Design with installation by Centerline Tile and Stone
Wicanders cork flooring via Amorim and All Tile Inc.
Northwestern Glass Fab partitions and railings
Hirshfield’s paints
Cutek stains via Meteek
Building Supplies
Tanner Windows and Doors Passive House windows and Hella exterior motorized shades via Peak Building Products
Cambek Designer Doors insulated garage door
Plasti-Fab EPS and insulated concrete forms
Pro Clima membranes, tapes, and Lunos heat recovery ventilation via 475 High Performance Building Supplies
Stego soil gas barrier and tapes
Huber Wood Products sheathing and tapes
Blueridge Fiberboard sheathing
Metal Sales siding
Appliances and Systems
Bosch, Thermador and Whirlpool appliances via Warners’Stellian
Zehnder America Passive House heat-recovery ventilation
Mitsubishi Electric cold-climate heat pump systems
Lighting via TSR and Crescent Electric
Loxone building automation
Passive House Electrified
Have a look at Tim Eian's slide deck for the Passive House Network's Building Electrification Symposium on July 25, 2024, and the “Electrify Responsibly with Passive House Plus” iPHA lecture on November 6, 2024.
Topics
Our Motivation to Electrify
The Context of the Project
The Process of Electrification
Considerations for Electrification
Data
Challenges of Electrification
Successes
Opportunities
Read the Case Study on Passipedia with the Passivhaus Institut in Darmstadt
Certifications and Highlights
Certified Passive House Plus - Project ID 5894
HERS Score: -8
EPA WaterSense, pending
Super-insulated, airtight building envelope (0.22 ACH50)
Passive House windows with triple-pane glazing and fully automated exterior motorized shading
Thermal bridge-free detailing and construction
Whole-house, balanced, enthalpy heat-recovery ventilation system
Electric cold-climate air-to-air heat pump system for heating and cooling with dedicated dehumidification
Electric air-to-water hot water heat pump system with wastewater heat recovery and continuously insulated pipes
LED lighting throughout
12 kWp photovoltaic system on roof; grid tied (100% wind power)
Level-2 vehicle charging in attached garage
Accessible main floor design and visitability, zero-step entries
Durable earth and people friendly and reclaimed materials throughout
Sustainable landscaping and extensive stormwater management with rain gardens
Urban infill
Project Details
Architecture: Tim Delhey Eian, TE Studio
Construction: Tanner Construction with Tim Delhey Eian
Structural Engineering: Align
Mechanical: TE Studio
Certifications: Herz & Lang (Passive House Plus), DPIS (HERS)
Project: 2018 – 2020
Photography:
Corey Gaffer, Gaffer Photography
TE Studio
T. Alkatout (aerial photos)